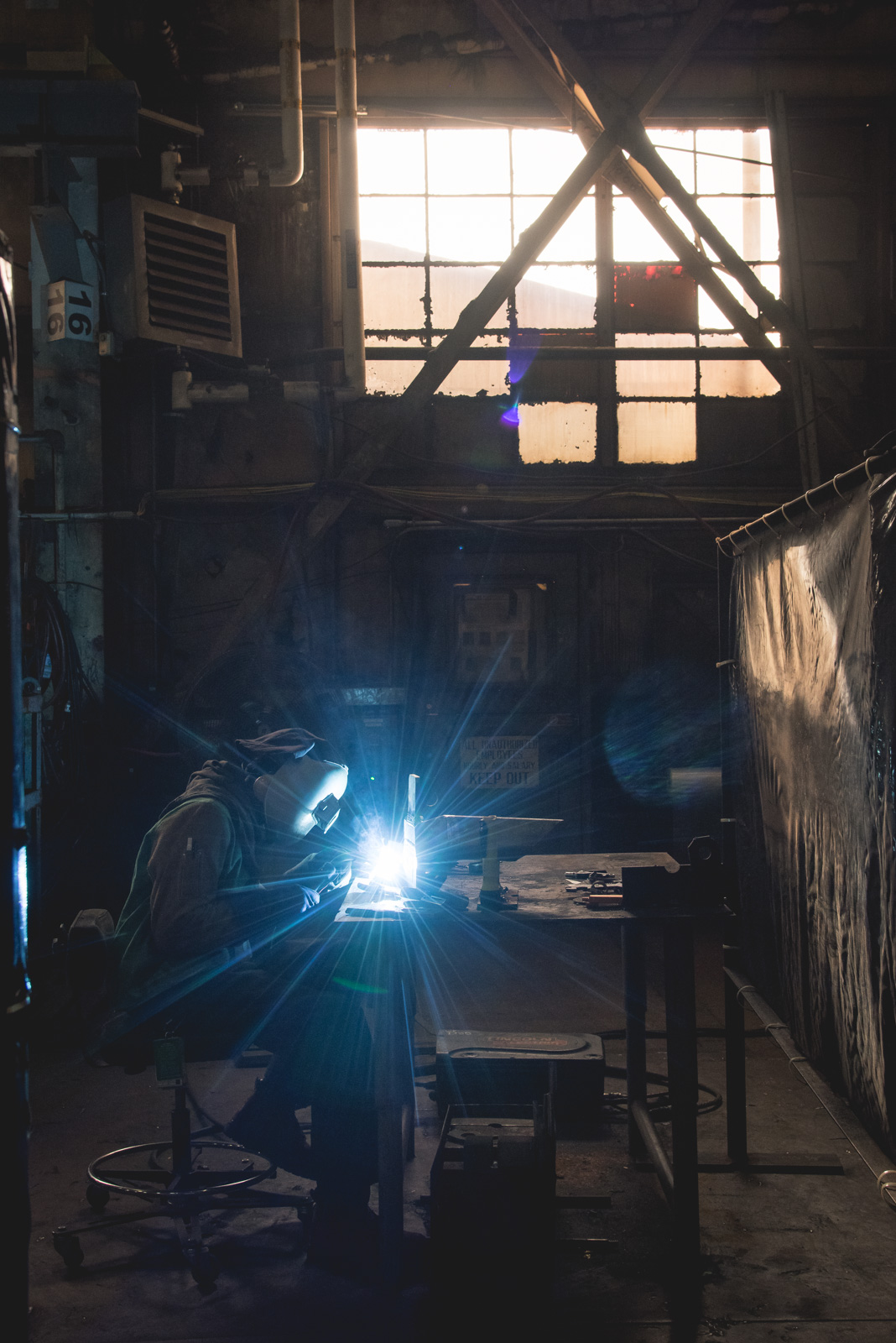
About a month after governments and employers began taking drastic actions to slow the spread of COVID-19, working from home and standing six feet apart at grocery stores have become rapidly the norm. But what about shipyard workers who cannot stay at home, who must work alongside colleagues to continue what has been deemed a mission-critical line of work?
Newport News Shipbuilding officials say their employees at their Virginia shipyard have found interesting ways to keep with the spirit of social distancing while also keeping their shipbuilding programs on schedule.
“Many of the jobs are one-man jobs, and six feet of social distancing is relatively easy to obtain. An aircraft carrier is a pretty big ship, and to spread a couple thousand people out on that, believe it or not, is not as hard as you would think. But there will always be jobs that will require individuals to do two-man jobs, and when we get to that point we have to think about the job differently,” Lucas Hicks, vice president of new construction aircraft carrier programs, told USNI News in an interview last week.
“When you can’t spread out, can you re-engineer your workspace? Sometimes it’s nothing more than enlarging a work platform; where my staging was very small, can I make my staging a little bit larger? Or if I had a containment to keep the component clean, could I make the containment a little bit larger? Could I use a tool extension? Could I use a GoPro with all the right security considerations to allow an inspector to see what I’m seeing real-time but from a distance of more than six feet away?” Dru Branche, the shipyard’s director of environmental, health and safety, said during the interview.
“And when you can’t spread out, then you want to kind of practice some form of shielding, and can you do that with gloves, with clear face shields? … Can you use a sheet metal or a Lucite (clear acrylic) or a Herculite (fabric) barrier between you and your coworkers that allows you to stop the spread of those respirable droplets that are what really cause the disease to spread?”
Branche said the company has a liberal leave policy in place and that some people have already moved from the day shift to the night shift, which allows for better spacing in construction areas and in office buildings. Several thousands of employees are also teleworking full time or a couple days a week, further thinning out the volume of people moving around common areas of the shipyard each day.
On Tuesday, the shipyard reported 14 cases of COVID-19. Jennifer Boykin, president of Newport News Shipbuilding, told local news outlets the yard is recommending employees wear cloth masks in line with CDC guideance.
Unique Approaches to Work
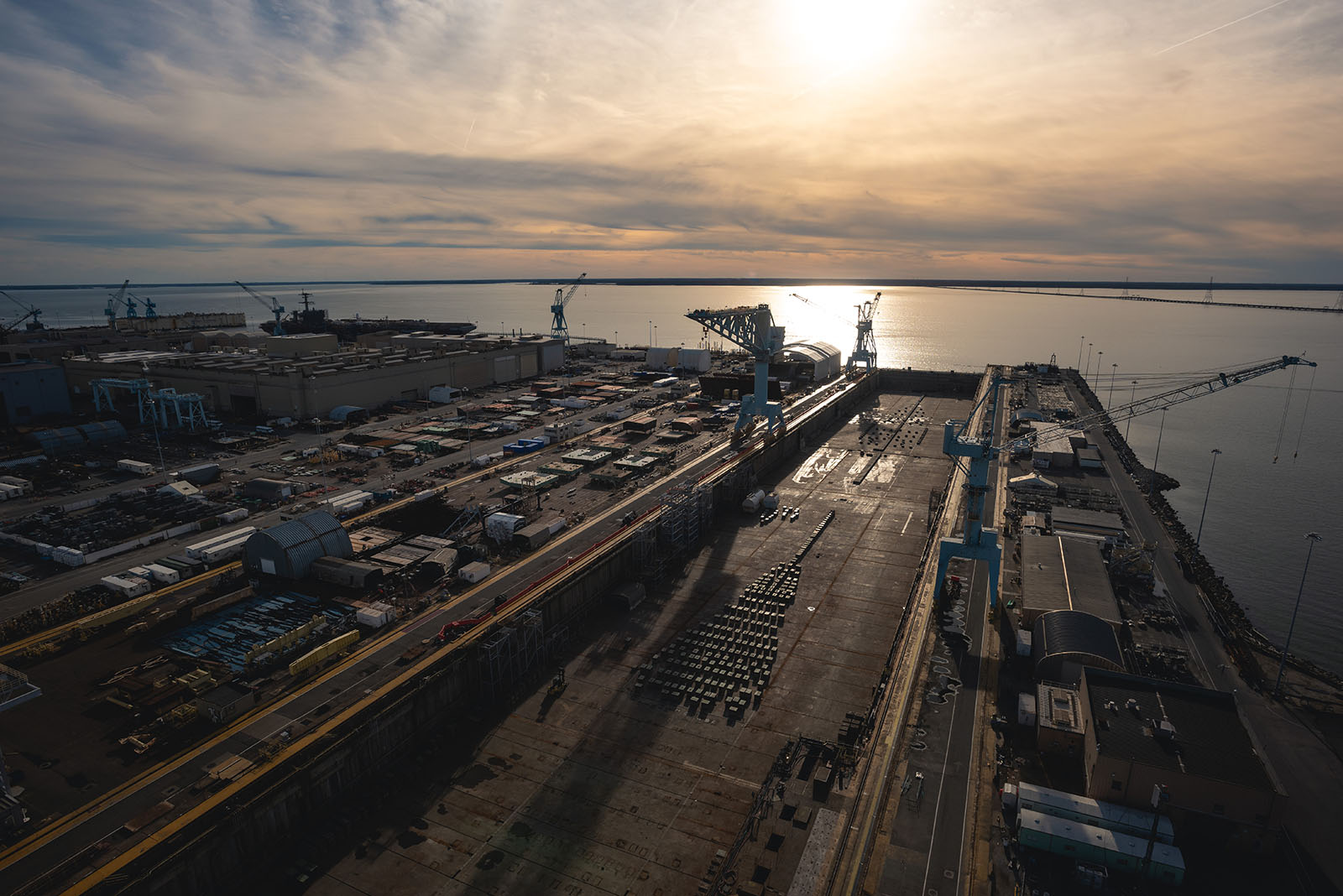
Hicks said the guidance health officials have given to the yard is to keep people six feet apart, and to limit time near one another to 15 minutes.
To achieve that, the workers are pulling tools out of the toolshed that allows them to work at greater distances. For example, many tools, such as grinders, have extenders that allow workers to access hard-to-reach spots on a ship.
“In normal circumstances, we would not employ such a device, but these are not normal circumstances. So we are looking at using existing tooling that gives us separation that we normally wouldn’t use in that application, but because we have them and can use them, we’ll apply them now in a different situation than we originally anticipated,” Hicks said.
He added that workers are being asked to be mindful of their jobs and consider alternate ways to carry them out. For example, if two people are required because one person is performing a task and the other has to inspect at each step along the way, the yard has determined that the two workers likely don’t need to be in a small space at the same time. Though it may slow down the work a bit, they’ve moved to one employee being in the space to perform a task and then stepping out before the inspector steps in.
Hicks noted an example from recent days, where three workers were supposed to be in a tent together, with the third person simply there for oversight.
“They said, well why don’t you cut a window in the tent so they could stand outside the tent? So they put a clear window in it,” Hicks said.
In select cases, the company is even allowing inspections to be done with the aid of GoPros and other camera gear.
“We are conservative in that approach, so if we believe it is a gray area then we’re going to do the hands-on visual” inspection, Hicks stressed.
“But if it is second-party verification that … an instrument may be taking a temperature reading or a pressure reading and [we need] second-party verification of that, the first party standing there doing it, the second party can do that effectively with a video assistant. No different. Now if it’s a five-times visual inspection of a weld, we wouldn’t do that with a video device, we would do that with eyes because we couldn’t ensure the magnification of the video device and things like that. So some of it we can and some of it we cannot.”
When there are no tools or workarounds to keep two people more than six feet apart, “where absolutely positively we can’t get around it, we one, either stop the job and look for a window downstream to go do it – now, not knowing where the window is, looking downstream, is this a critical path job, is this not a critical path job, can we push this a few months from now and still meet our objectives? Some of the time that happens naturally. Some of the time is, no, let’s put a respirator on and let’s go work this with proper controls, engineered controls,” Hicks said.
In these cases, the workers are outfitted with respirators, face shields, gloves, and other personal gear to keep them from picking up or spreading germs.
Hicks said most employees already have gloves and face shields as part of their standard tool package, used during tasks like grinding or sanding or other routine work. Not everyone has a respirator, since they have to be fit to the individual, but Newport News Shipbuilding has enough in its storage to take care of its workers in the event that workarounds are not possible and they need to be in close proximity to another colleague.
In fact, Hicks said of the respirators, “we stock and we have a good supplier and so on and so forth, to the point that we’ve leaned in and helped out with our local hospitals to get them some of the necessary supplies that we would have had on stock.”
He said the yard also has a lot of Herculite tent material and clear Lucite that can be used for shielding, so there haven’t been many big spends on gear to keep workers safe.
Rebalancing Two Work Shifts
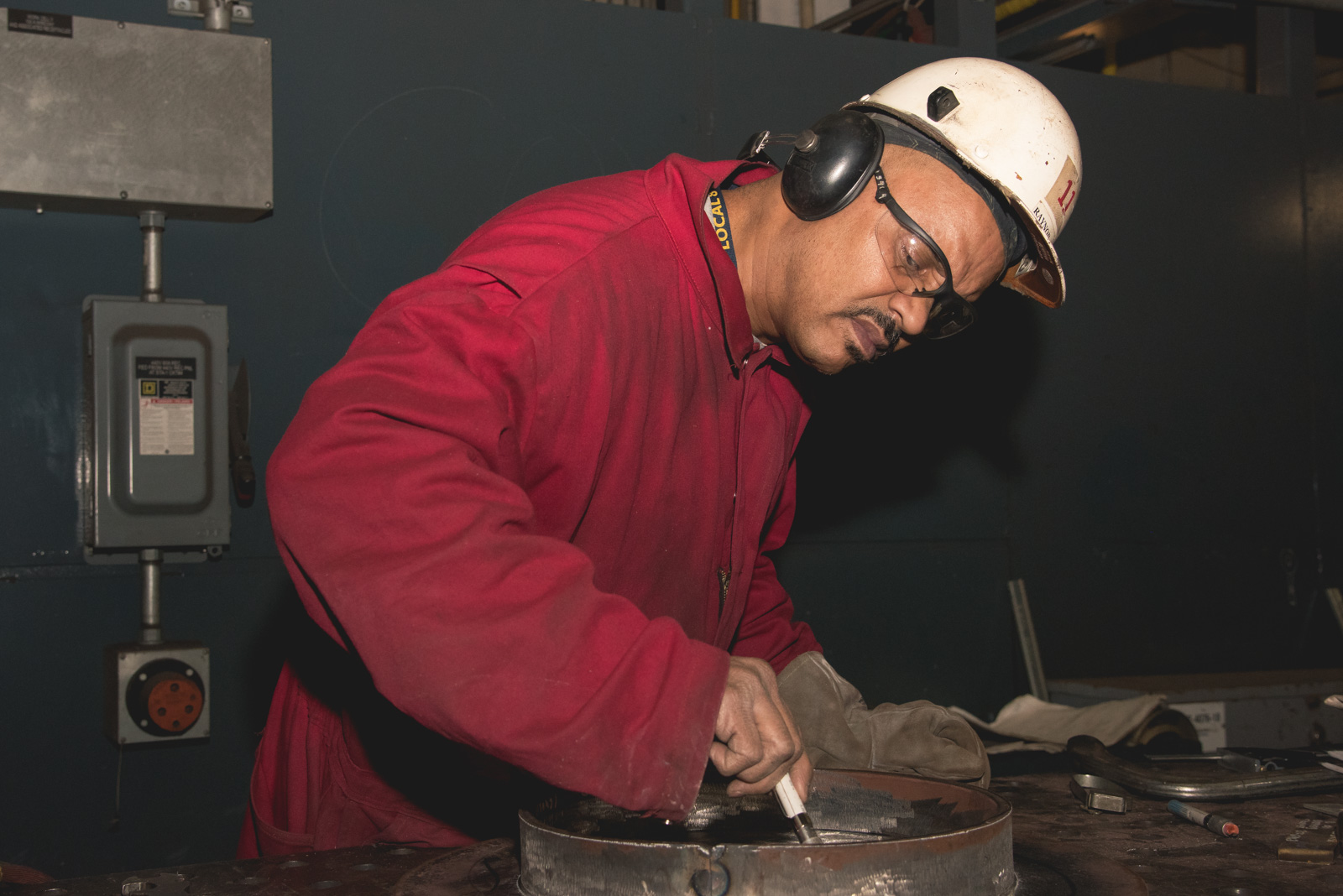
Hicks said the company has about 25,000 employees and that somewhere between 16,000 and 18,000 need to be in person at the yard.
To further spread out those people who need to remain at the yard for work, the company is trying to rebalance when work gets done. The yard typically runs a primary day shift and a much smaller back shift; Hicks said the company is trying to even out those numbers both to help out employees who may have children at home during the day now and to achieve the social distancing that health officials recommend.
“We are permitted to send entire crews to another shift by our collective bargaining agreement. But that’s not our intent. That’s just not our intention, we’re really trying to come through how to go enact this in the right manner. There’s a people piece of this that says, should you really go force someone onto the back shift? There’s also a people piece of this that says, in order to increase social distancing, we need to force people into the back shift. And we’re trying to come through what is the right way to deal with that,” Hicks said.
He said he hopes they can achieve the right numbers voluntarily, but if they cannot get to the right people per square foot numbers they yard needs, then they may start ordering additional crews or individuals to alter their work hours.
Asked how long this beefed-up back shift will last, Hicks said it was hard to say at this point. The yard has been in touch with its sister yard, Ingalls Shipbuilding in Mississippi, as well as the General Dynamics Electric Boat yard in Connecticut that it partners with for submarine construction, to share ideas and best practices.
Hicks said the yard has modeled every scenario of how long this pandemic could last and how quickly the yard could resume its normal work hours, even modeling what it would look like to shut down altogether or to cease certain activities altogether.
“We’ve run every scenario. We have them all on the shelf ready to pull the trigger if we have to. We’re just not there,” in terms of committing to any particular scenario, though, Hicks said.
With so many unknowns, Hicks said it’s also hard to guess what the schedule or cost impacts may be to the submarine and aircraft carrier construction programs taking place at Newport News Shipbuilding today.
“I think it’s too early to think we have any schedule adjustments to make. Again, not knowing what tomorrow is, but it’s too early to think we have any schedule adjustments to make yet. Not to say we won’t. But we also are working with the various [Program Executive Offices] – I was on the phone with [PEO Carriers Rear Adm. Jim] Downey today, to make sure his priorities and my priorities are aligned and that I understand what the most important ship is, relative to aircraft carrier construction, for him. I know that my counterparts on the [Virginia-Class Submarine] team are doing the same with the submarine PEO … and all the way up to [Vice Adm. Tom] Moore at [Naval Sea Systems Command].”
Hicks said constant communication between the yard and its customers will ensure that available workers are put on the right projects, and that if something has to be sacrificed it’s volume work and not critical path work that more directly determines a ship’s delivery schedule. Once the workforce is back at 100 percent, he said, they can look at overtime and other options to make up volume work as needed.
Teleworking and Digitization
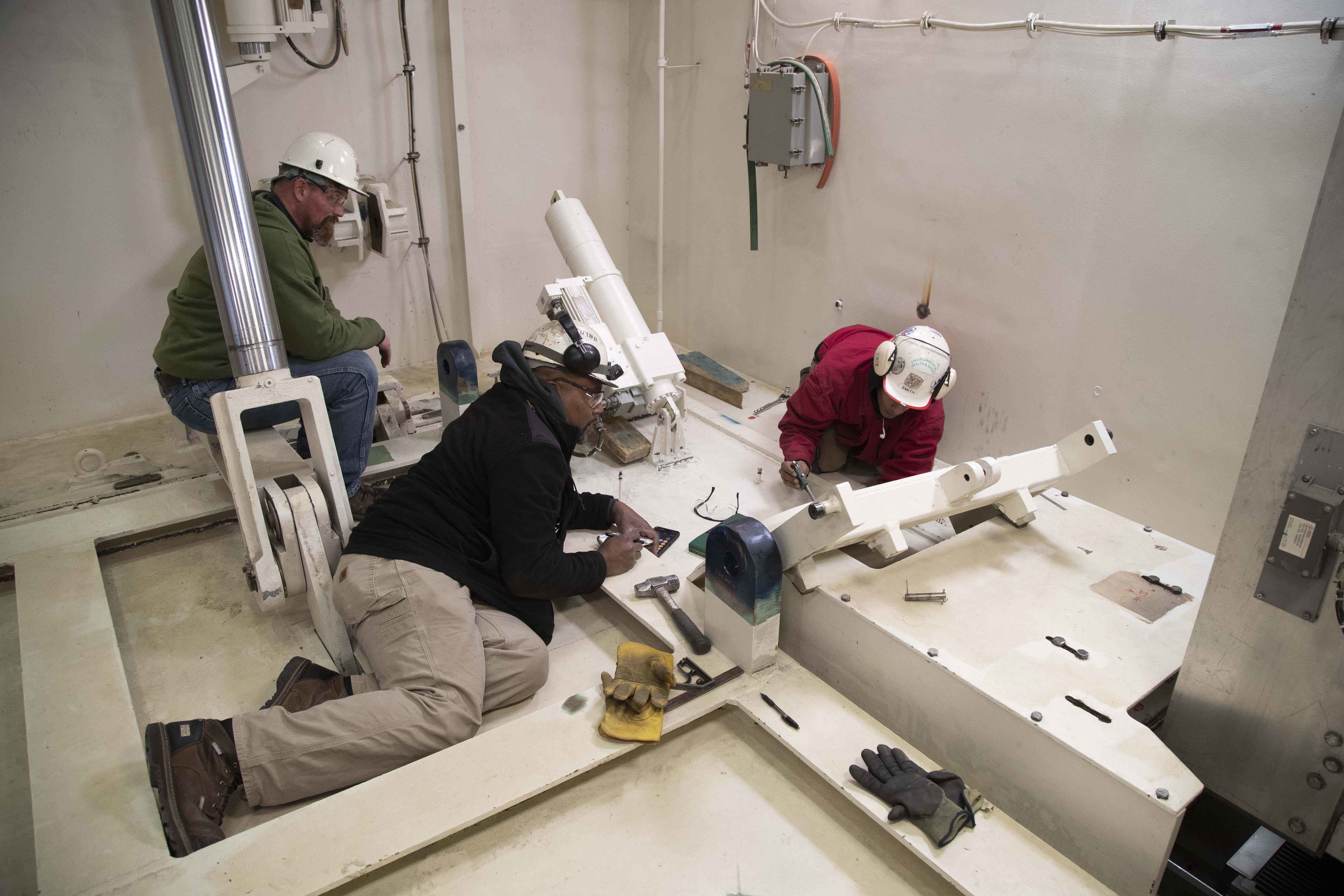
The shipyard happened to be in the midst of a digitization effort, with the future aircraft carrier Enterprise set to be the first ship built from fully digital plans instead of paper drawings. This effort has actually made mass teleworking go smoother than expected in a lot of ways, Hicks said.
“We are much better prepared than I think many of our peers may be” because of moves the company has made in recent years. The company already has 11,000 laptops deployed and bought 500 more to support teleworking employees. Designers, engineers and planners can work from home full-time because of the digital ship plans. Others, like financial analysts, have been able to divide into a blue/gold teaming model so they’re at work half the time and crunching numbers at home half the time, Hicks added.
Though the company has had some bandwidth limitations, and it realized early on it didn’t have enough phone lines, Hicks said they’re working through any challenges they encounter but are overall “in a much better spot” as a result of the move to digital. In fact, other than cleaning supplies, the additional laptops and network bandwidth have been the only real spending items for the company to support the yard’s pandemic response.
Additional Cleaning
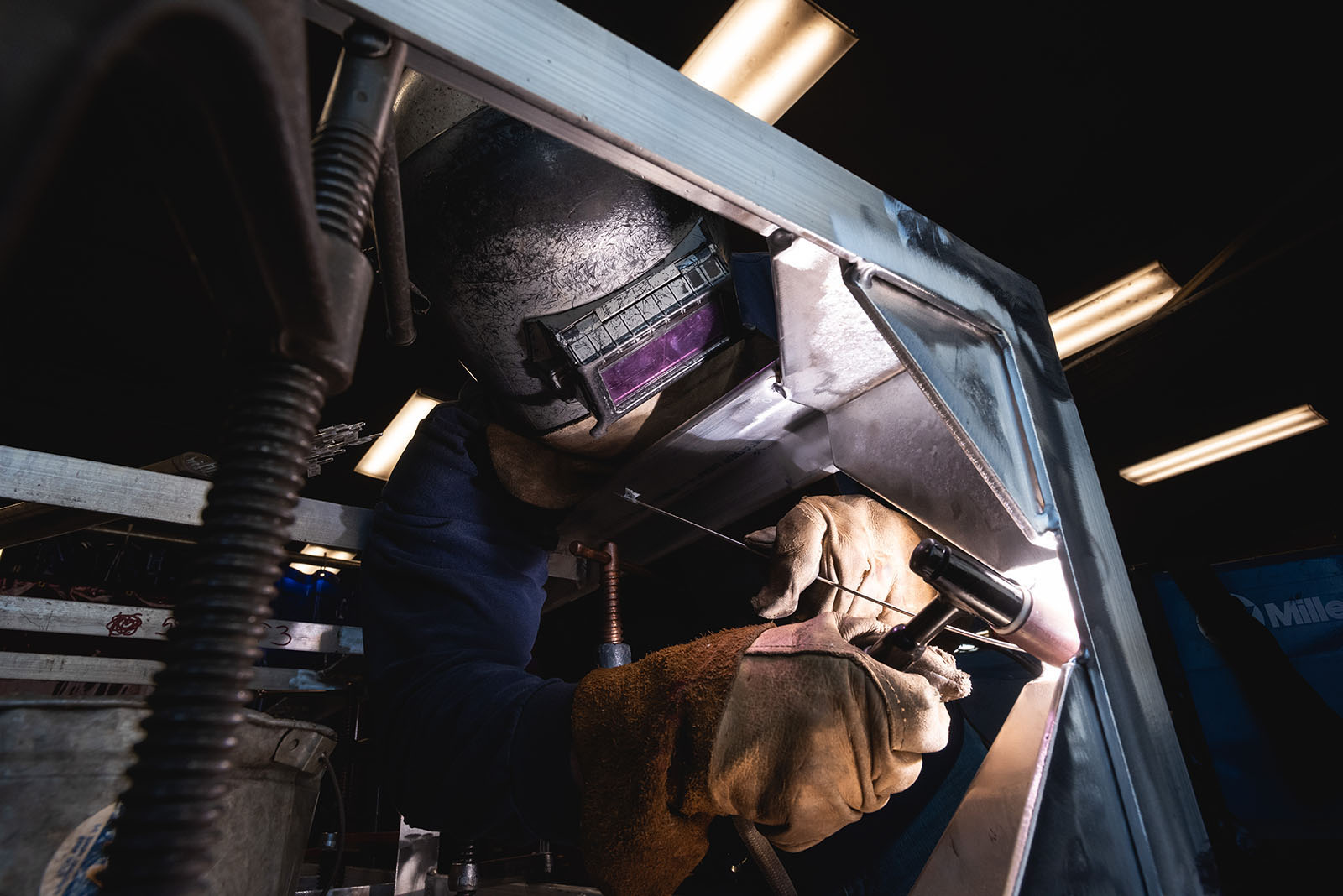
Branche said the shipyard had bought a range of products, from cleaners to aerosols to fogs, to disinfect all kinds of work spaces.
They’ve even developed “a newfound relationship – right at this second it’s a match made in heaven” – with an unusual nearby partner.
“We’re buying hand sanitizer from the local distillery that converted over from their traditional product line – which has been good, it’s not necessarily a neighbor we’ve done a lot of business with up until now, but it’s been super to have them so close,” she said.
Branche said it was hard to say how much more often spaces were being cleaned compared to usual, mostly because the employees themselves had begun wiping down bathroom countertops, door handles and other surfaces on their own, to keep themselves and their coworkers healthy.
She added the employees themselves had put up signs as well as marks on floors in places where people queue up – to get food, to get tools, to get drawings – and “just having the marking on the deck just kind of helps to say, oh yeah, this is where I have to stand,” has been very helpful.
“I think the shipbuilders themselves are taking this seriously, they’re leaning in and they’re trying to give themselves visual reminders to stay safe,” Hicks said.
“The fact that they’re leaning in like that is refreshing to me, as opposed to waiting for someone else to do it for them. They’re really taking ownership of this situation and their own personal safety.”